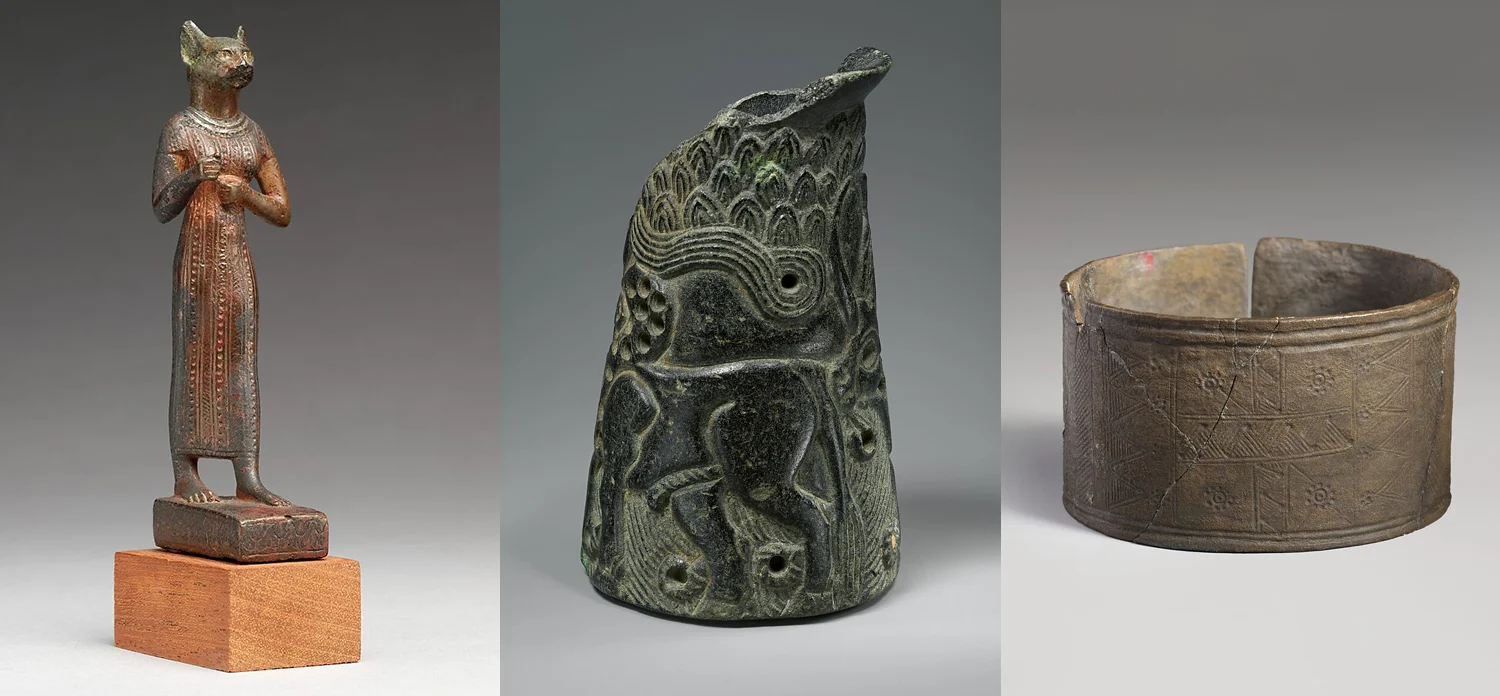
Join our community
Stay up to date with our top sellers, new trends and special offers by signing up for our emails.
The Bronze Age
December 10, 2024
Our Vice President/Creative Director, Cecil Adams, puts together the most fascinating forecasting and design briefs each year. For 2025, he predicts the Bronze Age will be flourishing as designers take inspiration from ancient cultures like those once found in Mesopotamia, Egypt, Syria, Iran, Thailand, and the Indus Valley, as well as the Mayan and Hittite civilizations. Textured metals in all categories top his list of trends; and with our fall releases, we have quite a few accessories, furniture pieces, and light fixtures that slide seamlessly into the mix.
The Bronze Age Trend
Making the ancient seem modern is a rallying cry of this predilection, as is being inspired to create something based on the time-honored. Cecil notes how bronze colorations complement warm neutrals, and he advocates for a fresh look at cave paintings, cuneiform writing, and ancient etchings for motifs. “Materials include hand-forged metals that are bronze or look like bronze, sand-blasted glass, terracotta, stone, wood, and rope,” he explains. “Textures include rough stone and terracotta, hammered metals, sand-blasted wood, carved details, stamped patterns, and rough glass.” Look to ancient sculpture and household items from antiquity like pitchers, urns, and bowls for soulful shapes to add to interiors, and consider the human form and motifs from nature as inspiration.
As for patina, he says, “Finishes include bronze, patinated bronze, washed gold, sanded recycled glass, natural woods, and surfaces that appear to the eye as if they are ‘unfinished.’” Think about archaeological digs to identify objects that appear they could have been discovered underground. Metal is one of the most enduring materials, even when buried in the earth. Examples of bronze’s durability abound as coins, sculptures, and masks continue to be unearthed each year. Like cultures of old, we take great pride in having works crafted by artists, which are then made into sculptures, accent tables, and lighting. We introduced seven bronze objects during the October 2024 High Point Market that are made with a lost-wax casting method or cire perdue in French. Each of them artfully illustrates this post, along with a number of others that have become some of our most popular items.
Bronze’s Beginnings
So what is the history of this wonderful metal material? Six thousand years ago is when we begin with the development of bronze in the Indus Valley, which is today’s Pakistan and northwest India. Bronze is a mixture of copper and tin in various proportions that are heated so that they bond on a molecular level to form a harder and more durable material. Bronze was first used for agricultural tools, military weapons/armor; and later for coins, cultural artifacts, and art objects. The Bronze Age, which was named after the then revolutionary new material, began in the eastern Mediterranean and continued to flourish there for quite some time. The lost-wax method of casting remained wide-spread in Europe until the 18th century when a piece-molding process became more predominant. The steps our artisans take to cast our bronze pieces are fairly straightforward, though the process today varies from foundry to foundry. There are two methods that are used, direct and indirect ones, both of which are described below.
The Indirect Method
During the indirect method, an artist or mold-maker creates an original model from wax, clay, or any material that will be able retain its softness. A mold his then made that is the exact negative of the original model. These inner molds are usually made of latex, polyurethane rubber, or silicone—materials that are supported by the outer molds, which can be made from plaster, fiberglass, or any number of durable materials. Most molds are made in at least two pieces, and a shim with keys is placed between the parts during construction so that the mold can be put back together accurately. When the mold is finished, molten wax is poured into it and swished around until it evenly coats its inner surface. Once the desired depth is achieved, the rest of the wax is poured out, the mold is turned upside down, and the wax layer is left to cool and harden.
When it has firmly set, the hollow wax copy of the original model is removed from the mold. After it is freed from the outer structure, the hollow wax copy is “chased” with a heated metal tool that is used to rub out the marks that show the parting line or the flashing where the pieces of the mold came together. The wax is then dressed to hide any imperfections and should by now look like a replica of the finished piece. Any pieces that were molded separately are heated and attached, and, at this point in the process, foundries often use registration marks to indicate exactly where they go. Finally, the wax copy is sprued with a treelike structure of wax that will eventually provide paths for the molten casting material to flow and for air to escape. The carefully planned spruing usually begins at the top with a wax “cup,” which is attached by cylinders to various points.
The Direct Method
During the direct method, a sprued wax copy is dipped into a slurry of silica, then into a sand-like stucco or dry crystalline material of a controlled grain size. This forms a shell that is allowed to dry before the process is repeated. This happens over and over until at least a half-inch coating covers the entire piece—the bigger the piece, the thicker the shell must be. With the direct method, the cup comes into play now, its inside left uncoated and its flat top serving as the base upon which the piece stands during the firing process. The core of each piece is now filled with fire-proof material before a step called the burnout takes place, at which point the ceramic-coated piece is placed cup-down in a heated kiln that hardens the silica coatings into a shell. As this transformation happens, the wax melts and runs out to leave the negative space that was occupied by the wax before it became fluid.
The shell is allowed to cool and is tested to see if water will flow freely through the feeder and vent tubes that were previously attached; and any cracks or leaks are patched with thick refractory paste at this point. To test the thickness, holes can be drilled into the shell, then patched. During the next step, called pouring, the shell is reheated in the kiln to harden the patches and remove all traces of moisture, then placed cup-upwards into a tub filled with sand. Metal is melted in a crucible in a furnace, then poured carefully into the shell, which has to be hot because the temperature difference would shatter it if it were not. The filled shells are then allowed to cool before they are hammered or sand-blasted away, releasing the rough casting. During the next step, called metal-chasing, the wax copies are chased the same as they are in the indirect method and the casting is worked until the tell-tale signs of the casting process are removed. Pits left by air bubbles in the casting and the stubs of the spruing are filed down and polished.
Artisanal Wrap-Up
A general rule of thumb is that a mold will usually last for the creation of only five pieces. Afterwards, it is too damaged so a new one has to made. This may seem laborious until you consider some artists, like Auguste Rodin, only created one piece from each mold before breaking it down. Though this is a great deal of information to absorb, the descriptions of these painstaking processes illustrate why our cast products in bronze are so valuable. If you’d like to give the gift of artisanship this holiday season, bronze sculptures will become prized possessions for anyone who appreciates fine art and will be treasured for decades to come.
The links to the wallpaper companies who supplied out backdrops are Thibaut and Fine and Dandy Company. Our cast bronze products that are shown are: in the first image, the Pelican Bronze, the Rotterdam Bowl, the Amsterdam Tulip Vase, the set of Utrecht Objects, and the Tunis Accent Table. In the second image, the Standing Black Panther Bronze, and in the last image above, the Herons on a Branch Bonze.